Amparo Vázquez: "We are ready to produce Electronics in Mold and we are just waiting for the OEMs to validate it".
It has been more than two years since Industrias Alegre announced that it was ready to integrate In-Mold Electronics into its production. Now the company has just signed an agreement with TactoTek, the leading company in smart surfaces, and demonstrates its commitment to a technology that can add a lot of value to the vehicle of the future... and of the present. Amparo Vázquez, R&D&I director, tells us more about this strategic commitment and shows us what we can expect from this technology.
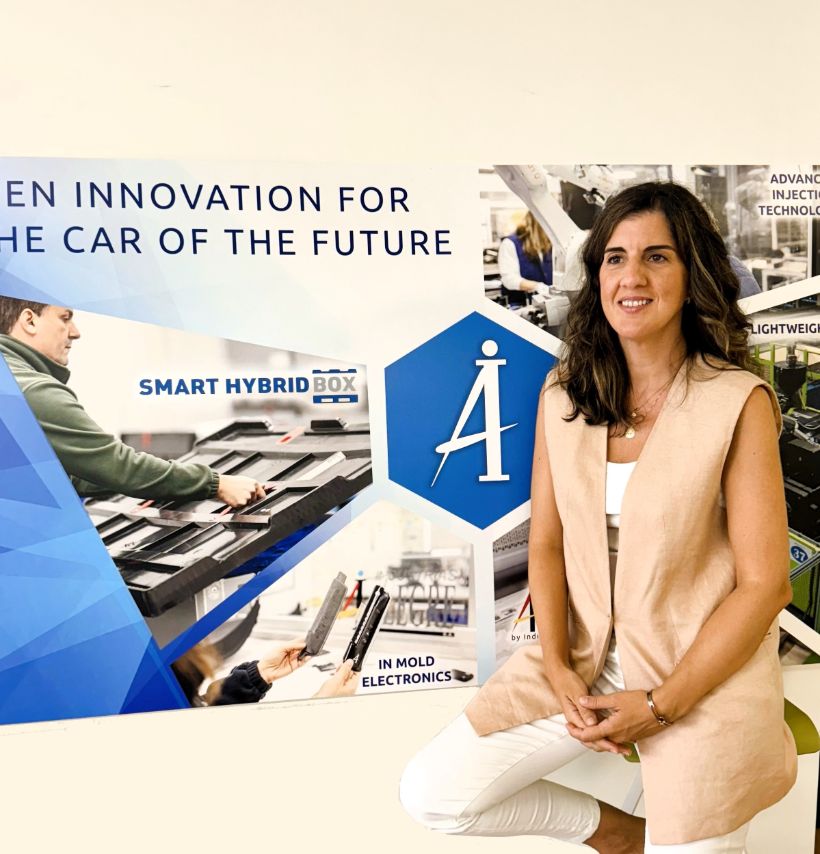
Question: It has been more than two years since you introduced your Electronics in Mold demonstrator. What has changed in this time in technology and industry?
Answer: Technology has been advancing throughout this time, of course, because there are many aspects involved in the design of a part with integrated electronics and there is a lot of room for innovation. On the part of Industrias Alegre, we have become aware of the state of maturity of this technology in a market as specific as the automotive market.
Q.: Is the automotive sector ready to incorporate this new technology?
A: This technology is already viable. The challenge now is to adapt it as quickly as possible to the requirements of the automotive industry, of which there are many. For our part, we have to wait until the OEMs validate it and accompany them in this process. We know that it is a long road, because they have to take into account many regulations, carry out many safety tests and all this while maintaining their high demands in terms of surface finishes. To sum up, I would say that the technology is ready to be used and we are just waiting for the OEMs to validate it.
Q.: And once you validate the technology, will you start demanding it?
A.: It is the most predictable thing. If you disassemble a product with conventional assembled electronics (whether it is an automotive product, a household appliance or a computer) and count all the components it has, you will see the production effort involved: there are multiple parts that, of course, use several injection molds that are the responsibility of different partners; and these in turn must respond to specific logistics, with product, component and subcomponent codes. Then you have to add assembly tables, welding, different manufacturing processes... And add the environmental aspect, because in the same part you can find up to a dozen different raw materials that must then be recycled: polycarbonates, polyamides, ABS, chrome elements, membranes with rubber, resins...
Against that, you see a part with integrated electronics and you understand the value of its simplicity. And it is also a fully recyclable part. But first you have to validate and confirm that the embedded electronics meet safety, aesthetic and functional requirements. But mainly safety, because after all, the car is a risky item. And it is logical for OEMs to take a cautious approach because we are talking about passenger safety.
Q.: I. Alegre, could you move on to producing this type of pieces soon?
A.: Right now we have the capability to integrate everything. We can design the part, design the mold and integrate the films with the electronics to get a final part. Our work at this point is geared towards being able to validate the final part one hundred percent. And we are talking about a unit validation process.
Q.: What does the agreement with TactoTek mean for I Alegre?
A.: It means partnering with a company that is a leader in this technology and thus having access to all the knowledge they have been acquiring over many years and consolidating through patents. And that allows us to offer our customers the security they need. Thanks to this agreement, we will be able to manufacture with design standards that they have proven in many other fields, and that means being able to anticipate and decide what is going to work and what is not. It is, after all, an agreement to make the road faster so that, when OEMs start demanding this technology, we can respond quickly and start manufacturing immediately.
Q.: So it will all depend on the designers' imagination?
A.: First the validations have to come and, from there, our impression is that designers will be counting on this type of solution. To do so, they have to open their minds a little bit to the possibilities that this technique can offer them, and that also implies a process of adoption.
At the moment, one of the most feasible applications is the incorporation of lighting in the interior of vehicles. It is an element that, in a simple way, greatly enhances the car's interior aesthetics. And with the integrated electronics we can illuminate certain areas in a very subtle way but that provides a great sense of comfort. In fact, they say that lighting is the new chrome and replaces those shiny contours that a decade ago were an unmistakable sign of luxury. And that would be an immediate and low-risk application of In-Mold Electronics.
Q.: That means working in the immediate but thinking about the future.
A.: That's what the designers are doing, who are already thinking of the car as an extension of your home or office. Because, when the car drives itself, we can even stand with our backs to the road and, if we have the EMI, any surface of the vehicle could be susceptible to some interface that is built with great simplicity and on a very thin surface. It is true that the autonomous vehicle seems a long way off, but we are already thinking about it.
Q.: We are also talking about a big reduction in the carbon footprint, right?
A.: Reducing the carbon footprint consists above all in simplifying, in unifying the materials of a part so that it can be recovered and reused more easily. And, as I said before, it is not the same to use 10 or 12 different materials and several secondary processes - injection molding, painting, chrome plating, laser cutting, stamping, etc. - as it is to integrate In-Mold Electronics, which allows you to significantly reduce the weight of the part and its complexity. All this contributes significantly to the reduction of the product's carbon footprint.
Of all the R’s of recycling and circular economy, one of my favorite and fundamental, since it dictates the origin of the products themselves, is that of Re-thinking, that is, questioning to make products differently, innovating in form, simplicity, space, mode of use ... and thanks to this technology, interesting opportunities open up.
Q.: What is your assessment of the future after the signing of this agreement?
A.: It is a strategic opportunity that allows us to remain at the forefront of the manufacture of plastic parts and anticipate the needs of large automotive manufacturers. For Industrias Alegre, betting on this technology means a great leap, going from manufacturing parts with some functionalities, but inert, lifeless, to making parts that can do things, launch commands to the touch, illuminate. It is a leap that allows us to offer a great added value to our customers and open a path of great strategic value.