Savings of 2,200 hours, 250,000 kg of cardboard and 10.5 t of CO2. This is how Hybrid Box works for this company
Could we reduce the weight of their FLC containers? How much time could they save? And could we reduce their waste production? An auto parts manufacturing company needed to increase its fleet of dedicated containers. But first it wanted to make sure it made the right choice. We did a quantitative analysis on their side and these are the results.
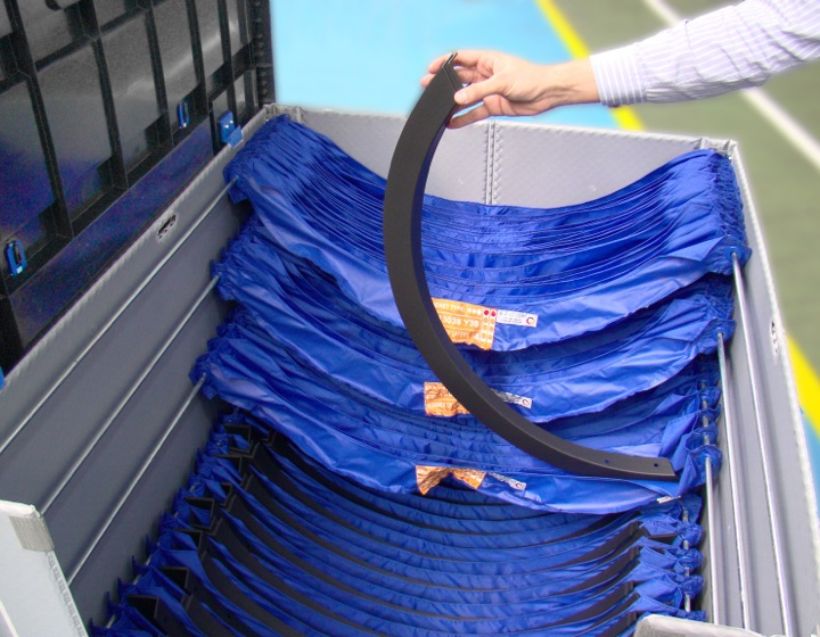
This company has a habit of quantifying before deciding. It follows Lord Kelvin's maxim to the letter and measures everything to improve day by day.
Our dedicated container versus a conventional FLC
When we started studying your case, we already had some very relevant data identifying the advantages of our dedicated HybridBox container over conventional FLCs. These are the concrete figures:
- 41% less in weight
- 30% less height (folded)
- 8% less in height
- 70% less assembly time
To this we had to add the other major advantages of our proposal: greater cleanliness, adaptable pockets, protection in critical areas, and the advantage that every day is seen as definitive: the possibility of completely eliminating single-use protective materials (films, foams or cardboard).
The data speak for themselves
But we wanted to go further, so we did the calculations with this potential customer. The results were definitive:
- 3,500 FLC-1210 containers released for other projects.
- 250,000 kg of protective cardboard eliminated per year
- 456 fewer trucks transported each year
- 2,200 hours saved each year in folding and unfolding containers
- 54% less weight transported each year
- 10.5 tons of CO2 no longer emitted each year.
The figures speak for themselves, would you like us to do the calculation for your company?