We present an industrialization process that ensures more efficient battery modules.
Making batteries more efficient is the challenge. The big challenge. The shape of the batteries and their chemical composition, the arrangement in the modules, the cooling... there are many elements that determine whether the final product can offer the required results. And one of the most important is the materialization of the modules. For this challenge, Industrias Alegre has already prepared a proposal of maximum precision. Do you want to know it?
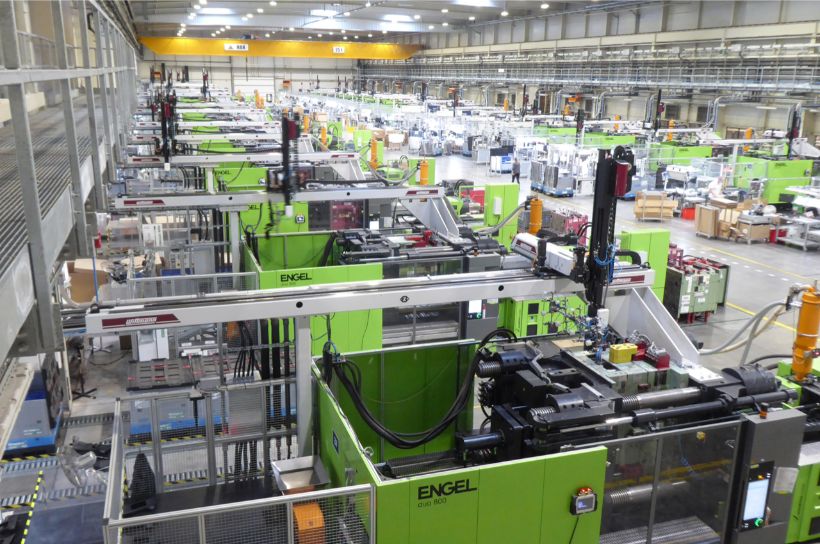
In electric mobility, batteries are much more than energy accumulators: they are the basis for the performance of new vehicles. And within batteries, the modules that make them up are much more than a mere physical assembly: they are the element on which scalability and efficient energy management depend.
That is why not just any module will do. For this part to contribute to a high-performance battery, its manufacture must be extraordinarily precise. And that is what Industrias Alegre is now proposing to the electrification and battery market: a process that contributes to improving its efficiency, charging capacity and durability.
From research to commercial proposal
At Industrias Alegre we delved into the reality of batteries with DETEBAT-VE, in mid-2021, a collaborative research that sought to develop an efficient battery capable of exceeding the requirements of the European 2030 regulations and which was led by the CMT Institute - Clean Mobility & Thermofluids of the (UPV). "In this project we took care of the design of the modules and for this we used polypropylene parts manufactured in 3D printer, which allowed us to adjust the designs until we achieved the best one", says José Pérez, engineer of our R+D+i team (you have more details of the project in this link). This research allowed our experts to know in detail all the requirements of the modules, of which there are many.
And with these learnings, the next step was to address this part technically, but now thinking about its large-scale industrialization. "To do this, it has been necessary to study various design and process proposals, facing different problems. We looked for and discarded solutions until we found the one we considered most suitable," says Miguel Alagarda, technical director of Industria Alegre.
Aluminum overinjection with highly reliable results
The proposal on the table today is designed for cylindrical cells. It is true that there are other proposals on the market (prismatic or pouch type) and that preferences may vary later on, but today this is the option chosen by the world leaders in electric vehicles, with Tesla and Lucid at the head. And for these cells, a reinforced plastic module with overinjection of aluminum inserts has been proposed. This basket-shaped part, into which the cylindrical cells fit, must offer high mechanical strength, avoid friction and ensure good heat dissipation. All this, with the lowest possible weight.
But overinjection of this part is not easy, as Alagarda explains. The first issue," explains Alegre's technical director, "is that we have to manufacture the entire module in a single injection and ensure that the lower part is completely clean of polymer, without any leaks". This is not a trivial issue because it is on this outer side where the connections between the modules and with the battery pack are located. The expected performance of the assembly will depend on the cleanliness of the injection.
Injecting vertically and ensuring perfect injection
The second production challenge is that of working with aluminum inserts that cannot be magnetized. "This situation we could solve with suction elements. We do it in many other cases. But this time we run the risk of less precise results or small deviations in the flatness of the base. And that is a risk we don't want to take because the slightest deviation has a knock-on effect on the final efficiency of the battery".
The proposal made by Industrias Alegre? To opt for vertical injection. Yes," continues Alagarda, "it is a less conventional way of injecting, which also implies having machinery that is practically made-to-measure, assembled especially for us. But it is the way to produce parts with the required quality".
After injection, the last step is to ensure insulation at the junction between plastic and aluminum, to prevent the creation of electric arcs or shunts that could constitute a safety risk in the module. The engineering expert goes on to explain: "We performed a 90-point weld on each of the modules to avoid the aforementioned risks, which is also critical for the efficiency of the battery. In this case, the biggest challenge has been to design a welding process with the necessary precision and point-to-point parameter control to guarantee the quality of the final part".
Process ready for industrialization
Vertical over-injection, controlled welding, assured flatness. It has not been easy, but we can now offer the market the high-precision manufacturing process that the new mobility is demanding.
Because the industrialization of batteries is taking off and making its way into the future. And at Industrias Alegre we want to be part of this exciting future.