Developing Artificial Intelligence for Waste Free Manufacturing
Artificial intelligence, such as that seen in ChatGPT, has burst onto the scene with an apocalyptic halo. But multiple tools that fit under the term “artificial intelligence” are here to stay and they are here to help us to improve production lines, among other things. This is our aim.
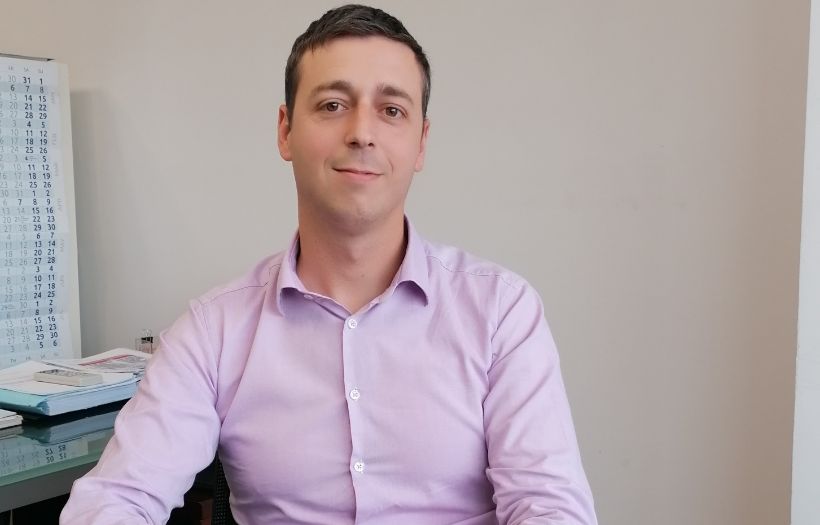
Industrias Alegres is part of the European project TEAMING.AI . We have joined the project with the objective of improving production by reducing errors and waste in injection processes with the help of predictive Artificial Intelligence. The priority is that this knowledge results in improved sustainability.
Bringing together Artificial Intelligence and Human Intervention
The innovation projects bring together the best of both worlds: predictive AI techniques working with experts and their experience. Our team boasts many hours of experience and has the valuable know how. Our goal is to take a giant step forward towards intelligent production.
Alejandro Espert, the AI-project coordinator within the team, explains to us how the project is developing:
"As in all AI processes, we started with electronic data capture during injection moulding. The significant parameters in manufacturing were discussed beforehand within the team and in great deal, which was necessary to start this process”. It is essential to choose the correct input data. This dataset is used as the fundamental basis to make predictions about deviations that normally occur during the injection process.
Data Planting to Make Predictions
The system can only make these predictions correctly once a considerable volume of data has been collected and has learnt to distinguish between defective pieces and pieces that are okay. This is where we are currently at in terms of the project’s progression. Our colleague sums up the progress made:
“For half a year now, we have been reporting daily on the injection data and real-time data provided by installed external sensors. And for more than two months, we have had a labelling system in place which indicates the to the system the pieces that are “ok” and “nok” (not okay). This is so the system can record the injection conditions that resulted in correct parts or errors. The next step will be for the consortium we are working with to send us the AI program that should be capable of anticipating and forewarning us before we inject a “nok” part.”
This is our aim: Artificial intelligence, using the data we have provided, can suggest to the operator in advance some machine settings meaning we won't produce defective pieces.
Will our software help us to limit material and energy loss? We are certain we will achieve our aim and, as is customary for this technology, it will continue to get better and better at making predictions. But only time will tell as we advance with the project.
Industry, academia, and software are united in the project.
To make this intelligent production line a reality, the innovation project brings together the different techniques of Knowledge Graph on a Machine Learning base. They are mechanisms of relational knowledge, which are quite normal in AI systems, and when incorporated with human collaboration, these tools improve both performance and precision and better resolve possible ambiguities. This is their contribution to more efficient industrial production.
Behind the effort is a group of businesses, technological institutions, and universities from 8 different countries, making a total of 15 participating members, committed to the improvement in production lines. Software Competence Center Hagenberg (SCCH) from Austria is the coordinating entity for the project, which includes three manufacturers: Industrias Alegre; Farplas, a company within the automotive industry, from Türkiye and Goimek, experts in precision machining, from the Basque Country in Spain.
Also, part of the consortium is the University of Mannheim, the Technological University Dublin and the Vienna University of Economics and Business. There are also the technological institutes Ideko and Itünova and a range of specialised companies, especially the following: Idea, Tyris, CORE, SD Partners, Timelex and Profactor.