"There are many automotive parts that are typically metallic that can be made lighter by transforming them into plastic"
If railroads and aeronautics are already choosing composite materials to lighten the weight of their carriages and fuselage, it is only a matter of time before the automotive industry joins this trend. To boost the electrification of automobiles and to limit the carbon footprint, which is a crucial aspect of the entire industry. But where exactly are we now, and what role does Industrias Alegre want to play in this area? We talked about all this with Amparo Vázquez, our R&D&I director.
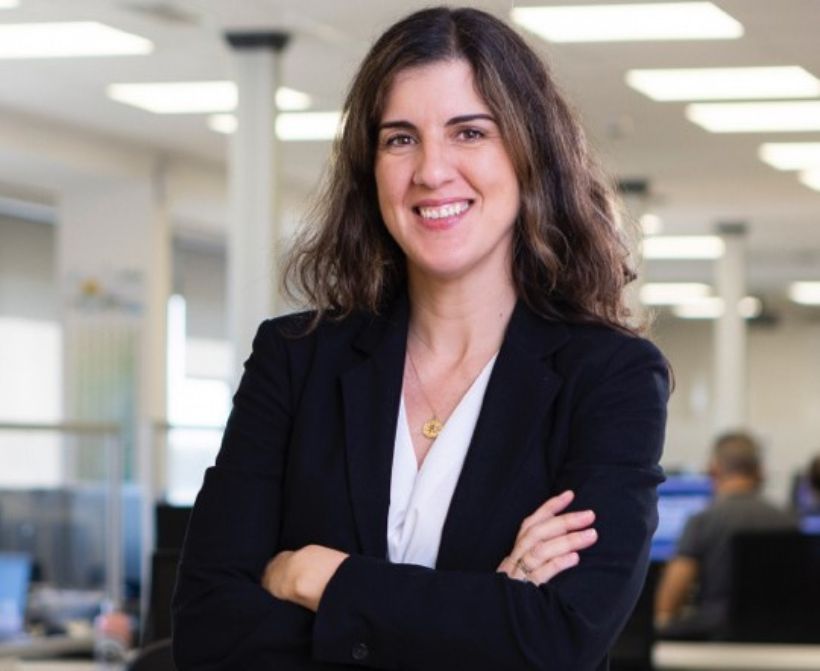
Question: Why does I. Alegre choose this moment to investigate the lightening of components, and how important is this aspect?
Answer: We are at a time when the approach to sustainability is multi-sectoral and is also crucial and mandatory. In particular, the relevance of the mobility sector, transportation in general, and its impact on the environment make it necessary to rethink each element in the value chain, each production process, each material used, the source of origin of that material, the right amount used with the least waste, and ultimately, how to achieve the same result with a lower consumption of resources.
At I. Alegre we approach lightweighting as a general concept; lightweighting is to reduce weight, to eliminate components, to reduce the number of references, to optimize.
Q.: The company already has experience in lightening components from design, but now will you focus exclusively on the use of new materials?
A.: No, we will continue to work on optimization from product concept and design, through material, components and manufacturing processes.
Q.: How much room for improvement do you think it is possible to achieve?
A.: If we are talking about replacing metal with plastic, it is possible to achieve improvements of between 40-50% weight reduction. If we consider lightweighting in the broad sense we have mentioned, optimization of materials, reduction of components... it is not easy to give a figure for the margin of improvement, but there is one.
Q.: You already have functional prototypes for manufacturing battery modules in plastic, are there many other parts that can change from metal to polymers?
A.: The importance of lightweighting in electric mobility is well known, hence battery modules and packs have been a good starting point to address these transformations, but this does not imply that research is reduced to these parts. The progress in the development of materials and technologies for the use of reinforced thermoplastic materials invites us to think that many other typically metallic automobile parts are susceptible to lightening with their transformation to plastic. Apart from the most critical references in terms of safety, we see it as viable to be able to compete with metallic solutions in many parts.
Q.: Recently, Airbus presented its A350 with a fuselage made mostly of composite materials: are we going to see something similar with automobiles?
A.: At the last JEC fair in Paris, which we attended in April, we were also able to see a Talgo carriage made entirely of composite materials. So, if it has already reached aeronautics and railroads, it seems obvious that sooner or later it will reach the automotive industry.
These solutions have always been far from the automotive sector because of their high costs, but the development of cheaper materials and the use of production technologies with higher production rates make composite materials increasingly competitive and bring them closer to the sector. In addition, lightweighting is becoming particularly important with the advent of electric vehicles.
Q.: Your research project aims to link lightweighting with decarbonization. How are you going to tackle these challenges together?
A.: Decarbonization is the main task of any manufacturing company today, and it must be promoted throughout the value chain to ensure an improvement for the planet. Lightweighting, in the full spectrum of the term, already means savings in terms of carbon emissions. Whether in terms of material savings, the use of 100% recyclable materials, or savings in transport consumption, among many other benefits.
Q.: What specific projects are you developing now?
A.: We have recently completed the LIGHTCAR project. In it, we have investigated together with AIMPLAS and other entities in search of new materials and we will soon present the conclusions. And at this moment we are tackling, under the framework of PERTE VEC I, a new development in the same direction.