Amparo Vázquez: “Estamos listos para producir Electrónica en Molde y solo esperamos a que los OEM la validen”
Han pasado más de dos años desde que Industrias Alegre comunicó que estaba lista para integrar Electrónica en Molde en su producción. Ahora la empresa acaba de firmar un acuerdo con TactoTek, la empresa líder en superficies inteligentes, y demuestra su apuesta por una tecnología que puede agregar mucho valor al vehículo del futuro… y al del presente. Amparo Vázquez, directora de I+D+i, nos cuenta más detalles sobre esta apuesta estratégica y nos muestra lo que podemos esperar de esta tecnología.
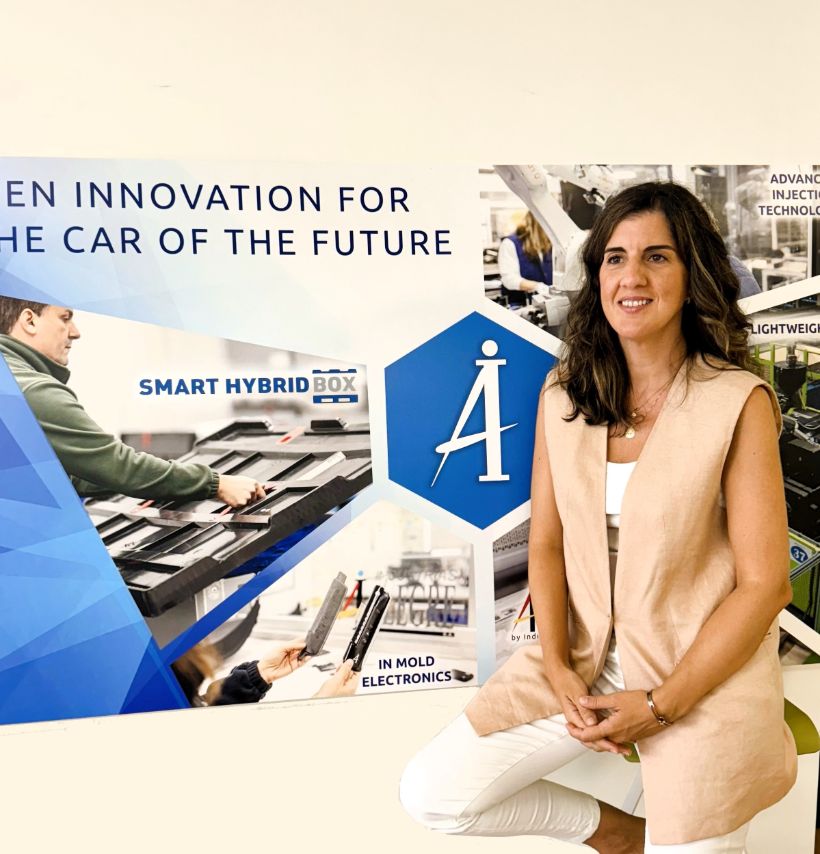
Pregunta: Desde que presentasteis vuestro demostrador de Electrónica en Molde han pasado más de dos años. ¿Qué ha cambiado en este tiempo en la tecnología y la industria?
Respuesta: La tecnología ha ido avanzando a lo largo de este tiempo, por supuesto, porque son muchos los aspectos que intervienen en el diseño de una pieza con electrónica integrada y hay mucho campo para la innovación. Por parte de Industrias Alegre, hemos tomado conciencia del estado de madurez que esta tecnología tiene en un mercado tan concreto como el de la automoción.
P.: ¿El sector de la automoción está dispuesto a incorporar esta nueva tecnología?
R: Esta tecnología ya es viable. Ahora el reto es adaptarla lo más rápidamente posible a las exigencias de la automoción, que son muchas. Por nuestra parte debemos esperar hasta que los OEM la validen y acompañarles en ese proceso. Sabemos que es un largo camino, porque deben considerar muchas normativas, realizar muchos ensayos de seguridad y todo ello manteniendo sus altas exigencias en cuanto a los acabados superficiales. Por resumir diría que la tecnología está lista para ser utilizada y solo esperamos a que los OEM la validen.
P.: Y una vez que validen la tecnología, ¿comenzarán a demandarla?
R.: Es lo más previsible. Si en este momento tú desmontas un producto con electrónica convencional ensamblada (da igual si es de automoción o un electrodoméstico o un equipo informático) y contabilizas todos los componentes que lleva, vas a comprobar el esfuerzo productivo que implica: ahí hay múltiples piezas que, por supuesto, utilizan varios moldes de inyección que son responsabilidad de diferentes partners; y estos a su vez deben responder a una logística concreta, con códigos de producto, de componente y subcomponente. Luego a ello hay que añadir mesas de montaje, soldadura, diferentes procesos de fabricación… Y agregar el aspecto ambiental, porque en la misma pieza puedes encontrar hasta una docena de materias primas distintas que luego se deben reciclar: policarbonatos, poliamidas, ABS, elementos cromados, membranas con goma, resinas…
Frente a ello, ves una pieza con electrónica integrada y comprendes el valor de su sencillez. Y además es una pieza reciclable en su totalidad.
Pero antes hay que validar y confirmar que la electrónica embebida cumple con los requisitos de seguridad, los estéticos y los funcionales. Pero fundamentalmente de seguridad, porque después de todo el automóvil es un artículo que entraña riesgos. Y es lógico que los OEM vayan con pies de plomo porque hablamos de la seguridad de los pasajeros.
P.: I. Alegre ¿podría pasar ya a producir este tipo de piezas en breve?
R.: En estos momentos tenemos capacidad para integrarlo todo. Podemos diseñar la pieza, diseñar el molde e integrar los filmes con la electrónica para obtener una pieza final. Nuestro trabajo en este momento se encamina a ser capaces de validar la pieza final al cien por cien. Y hablamos de un proceso de validación unitaria.
P.: ¿Qué significa para I Alegre el acuerdo con TactoTek?
R.: Significa asociarnos con una empresa que es líder en esta tecnología y, así, tener acceso a todo el conocimiento que ellos han ido adquiriendo a lo largo de muchos años y que han ido consolidando a través de patentes. Y eso nos permite ofrecer a nuestros clientes la seguridad que necesitan.
Gracias a este acuerdo, podremos fabricar con unos estándares de diseño que ellos han probado en otros muchos campos y eso significa ser capaces anticiparnos y decidir qué es lo que va a funcionar y qué no.
Se trata, después de todo, de un acuerdo para hacer más rápido el camino y que, cuando los OEM comiencen a demandar esta tecnología, nosotros podamos dar una respuesta rápida y comenzar a fabricar de forma inmediata.
P.: Entonces ¿todo dependerá de la imaginación de los diseñadores?
R.: Primero tienen que llegar las validaciones y, a partir de ahí, nuestra impresión es que los diseñadores van a ir contando con este tipo de soluciones. Para ello tienen que abrir un poco la mente a las posibilidades que les puede aportar esta técnica y eso también implica un proceso de adopción.
De momento, una de las aplicaciones más factible es la incorporación de iluminación en el interior de los vehículos. Es un elemento que, de una forma sencilla, potencia mucho la estética interior del coche. Y con la electrónica integrada podemos iluminar ciertas zonas de forma muy sutil pero que aporta una gran sensación de confort. De hecho, dicen que la iluminación es el nuevo cromo y viene a sustituir a esos contornos brillantes que hace una década eran señal inequívoca de lujo. Y esa sería una aplicación de la Electrónica en Molde inmediata y de bajo riesgo.
P.: Eso implica trabajar en lo inmediato pero pensando en el futuro.
R.: Es lo que hacen los diseñadores, que ya están pensando en el coche como una extensión de tu casa o tu oficina. Porque, cuando el coche se conduzca solo, podremos estar incluso de espaldas a la carretera y, si contamos con la IME, cualquier superficie del vehículo podría ser susceptible de contar con alguna interface que se construye con gran sencillez y sobre una superficie muy fina.
Es cierto que el vehículo autónomo parece que está muy lejos, pero ya estamos pensando en él.
P.: Hablamos también de una gran reducción de la huella de carbono, ¿verdad?
R.: La reducción de la huella de carbono consiste sobre todo en simplificar, en unificar los materiales de una pieza para que luego se pueda recuperar y reutilizar con más facilidad. Y, como decía antes, no es lo mismo emplear 10 o 12 materiales distintos y varios procesos secundarios —inyección, pintado, cromado, corte láser, stamping, etc— que integrar la Electrónica en Molde que te permite reducir significativamente el peso de la pieza y la complejidad. Todo ello contribuye de forma notable a la reducción de la huella de carbono del producto.
De todas las ERRES del reciclaje y la economía circular, una de mis favoritas y fundamentales, ya que dicta el origen en sí de los productos, es la de Re-pensar, es decir, cuestionarse el hacer los productos de forma diferente, innovar en la forma, en la sencillez, en el espacio, el modo de uso... y gracias a esta tecnología se abren interesantes oportunidades.
P.: ¿Una valoración sobre el futuro que se abre tras la firma de este acuerdo?
R.: Es una oportunidad estratégica que nos permite mantenernos a la vanguardia de la fabricación de piezas plásticas y anticiparnos a las necesidades de los grandes fabricantes de automoción.
Para Industrias Alegre, apostar por esta tecnología significa un gran salto, pasar de fabricar piezas con algunas funcionalidades, pero en sí inertes, sin vida, a hacer piezas que pueden hacer cosas, lanzar órdenes al tacto, iluminar. Es un salto que nos permite ofrecer un gran valor añadido a nuestros clientes y abrir un camino de gran valor estratégico.