En la carrera hacia la mejor batería para automoción, la fabricación aditiva ha demostrado su gran valor
Si hay urgencia, la fabricación aditiva tiene mucho que aportar. Y así lo ha demostrado nuestro equipo 3D a lo largo de DETEBAT-VE, un proyecto colaborativo en busca de la batería más limpia liderado por el Instituto CMT - Clean Mobility & Thermofluids de la Universitat Politècnica de València (UPV).
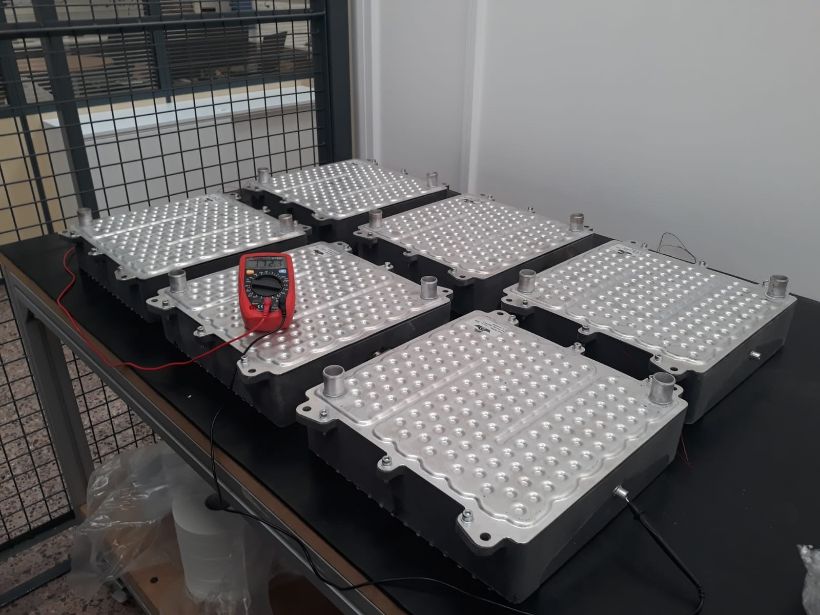
En este momento, la automoción vive una carrera por encontrar las baterías más eficientes, más sostenibles y producidas a mayor escala posible. Y, en este contexto se ha desarrollado el proyecto colaborativo de investigación DETEBAT-VE, un trabajo cuyo objetivo consistía en fabricar un demostrador a través del cual pudiéramos dar con un buen modelo de batería, que fuera eficiente y que tuviera el mínimo impacto ambiental posible a lo largo de su vida útil. La investigación ha implicado a muchos participantes, cada uno de los cuales ha aportado el conocimiento específico en un área.
“A nosotros nos correspondía ocuparnos de los módulos, las piezas contenedoras dentro de las cuales se incorporan las celdas y los sensores, y que van unidas al cooling plate”, nos comenta José Pérez, ingeniero de nuestra sección de I+D+i. Y continúa: “Los módulos son elementos que tradicionalmente fabricaban en hierro y que luego se aligeraron usando aluminio. Nosotros hemos utilizado el polipropileno, que aporta las características físicas requeridas y con el que conseguimos un aligeramiento de un 40 a un 50% con respecto al aluminio”.
La fabricación aditiva como un atajo
Sabemos que, a la hora de realizar una producción en serie, los módulos se fabricarían en inyección de plástico, que siempre resulta más rentable en tiradas largas. Pero con una investigación en marcha, la fabricación aditiva supuso tomar un atajo de gran valor, pues nos permitió obtener prototipos funcionales sucesivos en tan solo dos o tres días. Sin moldes. Sin esperas.
“El mayor reto del proyecto para nuestra empresa consistía en proponer el mejor diseño de la pieza logrando también que respondiera bien a las muchas exigencias físicas”, comenta Pérez. En este sentido ha sido crucial contar con la impresión 3D, “porque hemos podido ir haciendo pequeñas adaptaciones de diseño y, una vez definido este de manera definitiva, hemos podido contar con prototipos sobre los que se han realizado las comprobaciones necesarias, tanto mecánicas como térmicas, pues que funcione como retardante de llama es una de las necesidad clave en el ámbito de las baterías”.
Que el intercambio de ideas fluya
Poder meter la pieza en el laboratorio para ponerla a prueba sabiendo que este prototipo tiene las mismas características funcionales que la pieza que, en un futuro, puede fabricarse en inyección, ha sido una ventaja esencial en el proceso de investigación. “Incorporar este método de fabricación —comenta Pérez— aporta agilidad y sencillez a la investigación. Y, de ese modo, permite que el intercambio de ideas y de conocimientos en el equipo fluya mejor”. De hecho, hoy ya nadie de este equipo imagina lo que hubiera significado tener que esperar varias semanas a la espera de un molde de inyección antes de poder hacer verificaciones.
Esta ha sido nuestra experiencia con las baterías. Y tú, ¿qué investigación estás desarrollando? ¿te gustaría contar con prototipos funcionales en tiempo récord?